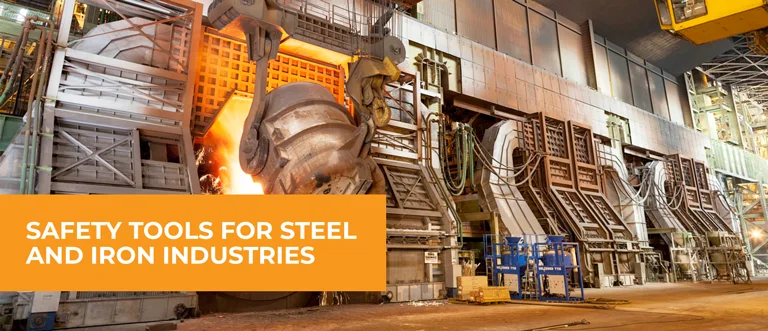
INSULATED AND NON-SPARKING TOOLS – A PREREQUISITE FOR STEEL INDUSTRY
Safety Guidelines for Iron & Steel Sector published by the Ministry of Steel, Government of India in 2019 and discussed how insulated tools and non-sparking tools are indispensable for both Integrated Steel Plants as well as in Mini Steel Plants / processing units.
Demand for steel in India is growing @ 7% per annum. We are the second largest producer of Steel and largest producer of Sponge steel in the world.
India has passed the National Steel Policy in 2017 which has laid the road map for the growth of the steel sector. Main aim is to build India’s crude steel capacity to 300 MT by 2030. This in itself requires huge investment in terms of capital as well as direct and indirect employment opportunities. As we build this capacity, safety of the people employed will be critical in achieving this target.
Occupational Safety & Working Conditions continues to be relatively neglected by the Indian industry. While India has approximately 3% share of global manufacturing, it has 30% share of the industrial fatalities globally. It is blatantly obvious that the overall success of the Indian Industry rests on having the lowest rates of safety incidents. While it may not be the only parameter, it would be unwise to assume that we can be global leaders with such high rates of fatalities. The safety guidelines issued by Ministry of Steel are meant as minimum guidelines to be followed and provides a basic framework.
For this article we enumerate a few hazards and how the correct choice of tools can help mitigate the risks. Hazards of interest identified by the guidelines are as per below:
Explosive Gases (Rich in Hydrogen and Methane)
As per the safety guideline explosive gases are present through a steel plant and pose the following risks:
Fire & Explosion
Steel Plants stores & handles number of flammable chemicals like tar, naphtha, benzol, fuel gases, oils, LPG, Propane, Oxygen etc. which possess potential fire & explosion hazards. Hot metal/ slag sparks, welding sparks, electrical short circuiting etc. can also lead to fire in surrounding areas if combustible materials are present.
Confined spaces
Bin, silos, tunnels, ESPs, manholes, etc. are examples of confined spaces where entry of persons & carrying out jobs requires special precautions. Toxic or flammable gases, oxygen displacement and engulfment are the principal hazards
Electric Shock, Electrocution, Flashover
The above hazard is present across the entire steel plant and the guide covers
Control of hazardous energy
The iron and steel industry regularly uses different sources of energy (electric, mechanical, hydraulic, pneumatic, etc.). The safe control of energy should be addressed by procedure and carried out by appropriately trained personnel in accordance with the nature of the energy source and the characteristics of the facilities.
To mitigate the various hazards 25 safety guidelines have been codified. We analyses specific guidelines and highlight the ones where non-sparking and insulated tools have been called for either directly or indirectly.
Storage, Handling & Use of Gas Cylinders (SG/01)
Section 3.6.d of this guide clearly states the following:
- Spark proof tools shall be used when working with or on a flammable compressed gas cylinder or system.
Any tool such as wrenches, spanners, pliers, etc used for maintenance of a cylinder or a gas system should be non-sparking.
For operation of (flammable) gas cylinders it is correct practice to us non-sparking cylinder keys for turning the valve on/off. As there may be some local leakage of gas around the outlet it is important to remove all sources of ignition. Using cylinder keys made from steel may introduce a source of spark that can ignite any leaked gas.
Electrical Safety (SG/15)
In the guide for Electrical Safety it is stated in Section 3.2.4.iv that:
- The tools & tackles like screw drivers, pliers, cleaning brushes, Hand lamps, torches etc. should be properly insulated
Electrical hazards that have been identified in the guide earlier are: shock, electrocution and flashover. Electrical shocks are the highest reported incidents in Electrical Safety. Hence, it is imperative to eliminate (or at least drastically reduce) electrical shocks in Steel plants. This alone would be a big step in safety. Electrical technicians use hand tools such as screwdrivers, pliers, wrenches, in maintenance of panels, busbar, electrical wirings, etc. within the various locations of the plant. As such they are at the highest risk of shocks and electrocutions. Standard operating procedure in any steel plant should require every electrical technician to carry a set of 1000V Insulated toolkit which has the most commonly tools used by them. A toolkit such as the below one should be available and used:
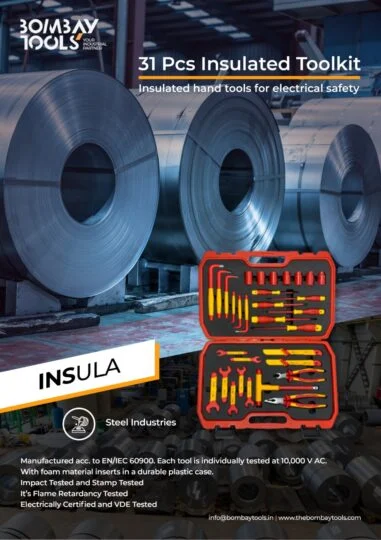
Another very severe hazard is a flashover. While flashovers are not as common as electrical shocks its severity necessitates its complete elimination. There have been several incidents of flashover where steel tools are known to have caused short circuits between high potential contacts. Usage of insulated tools can reduce risks of such shorting and prevent flashovers.
Fire Safety (SG/16)
The guideline for fire safety covers various fire prevention measures. Non-Sparking tools are indispensable in prevention of fires in many different areas within a steel plant. Below we enumerate where and why non-sparking tools are necessary
In section 3.3.3 (Fire Prevention Measures at Cylinder Storage Area) it should be standard practice to use *only* non-sparking tools if any maintenance or operations need to be performed in this area
Section 3.3.5 (Fire Prevention Measures for Diesel Storage Tank) states the following:
- Standard Operating Procedure (SOP) for loading and unloading of oil and emergency preparedness should be in place.
Any tools that are needed such as drum openers and bung wrenches should be non-sparking. If specialized tools such as hook wrenches are needed for couplings then the same should also be in non-sparking.
The above is also applicable for section 3.3.6 (Fire Prevention Measures for Propane Installation) during unloading operation of propane.
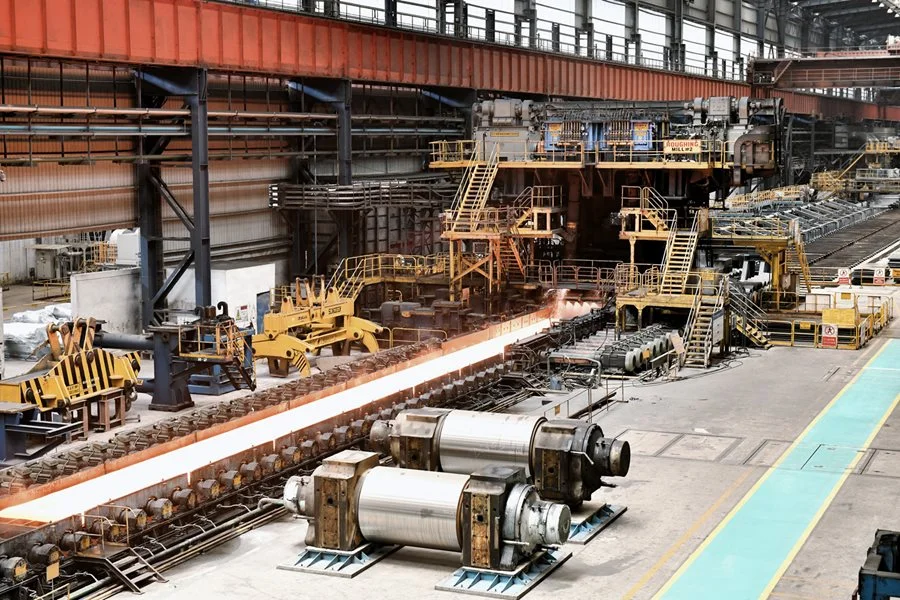